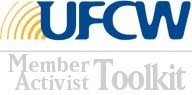
A public online Member Activist website, memberpower.ufcw.org, is available for local union staff, aimed at:
- Showcasing success stories from local unions who have worked with member activists in creative and innovative ways, and challenging staff to think outside the box when it comes to problem solving and strategy building.
- Providing workshops and training handouts for staff to recruit member activists and harness the power of their membership to achieve solid gains in the workplace and help win campaigns.
- Fostering a culture of solidarity and inclusion through workshops and actions that build bridges across different demographics and challenge member activists to consider their own perspectives and positions relative to their coworkers and fellow union members.
- Presenting best practices for member engagement on a variety of topics, including bargaining, safety and health, gender equity, right to work, and welcoming new members.
What Can Be Found on the Site?
A searchable database of sample materials from local unions, including trainings, handouts, leaflets, picket guides, and workshop outlines submitted by local union staff who have found them useful to engage their own members.